Siloxanes are abundant in modern times. These silicone-based compounds can be beneficial when used in cosmetics to soften, smooth, and moisten. They make hair products dry more quickly and deodorant creams slide on more easily. They are also used extensively in moisturizers and facial treatments. Siloxanes can also be found in medical implants, water-repelling windshield coatings, and building sealants and lubricants. We have even found them in the chemicals frackers inject into their wells.
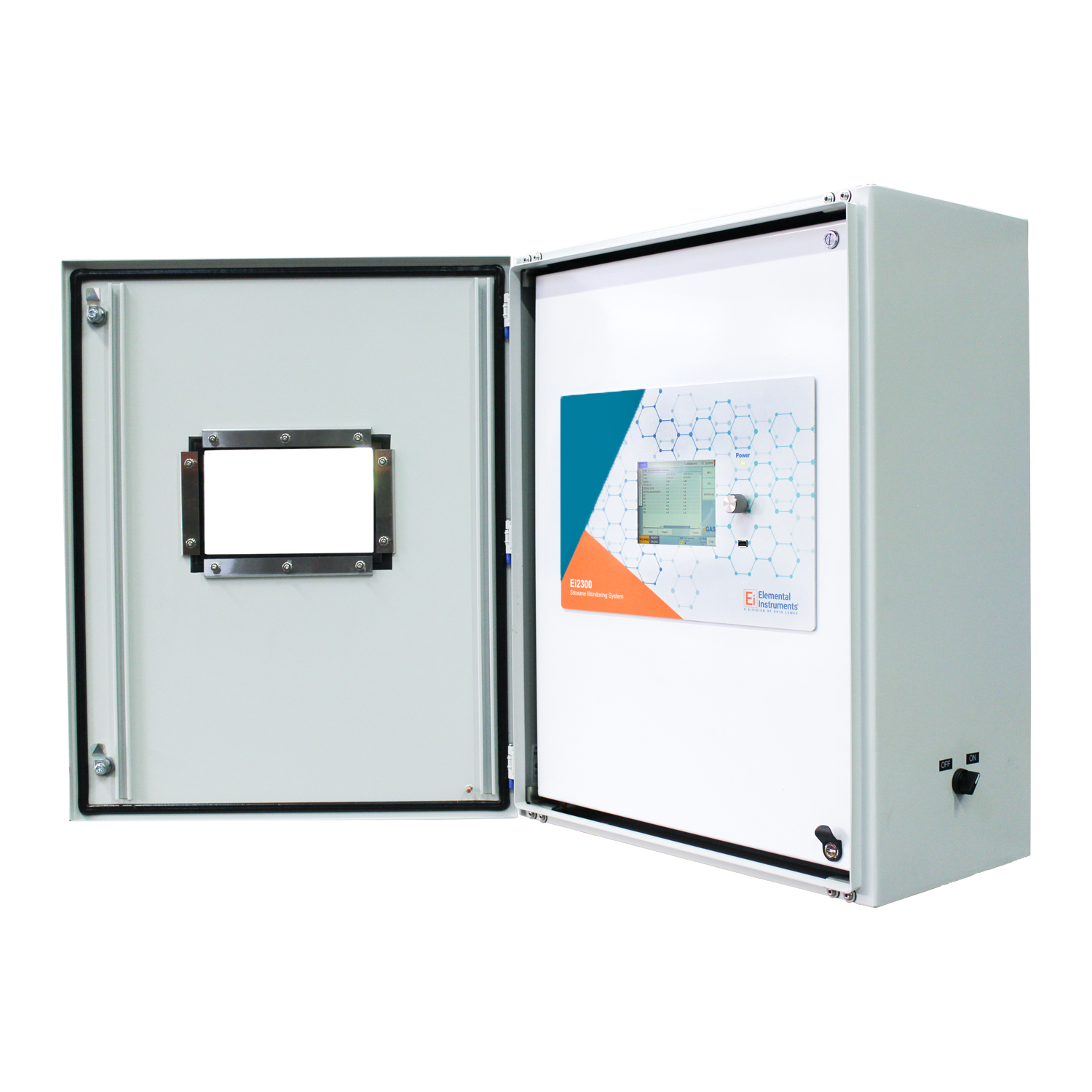
However, some industries such as landfills and wastewater treatment plants that use biogas to generate electricity, or upgrade the biogas to Renewable Natural Gas (RNG) for direct injection into a natural gas pipeline or to Compressed Natural Gas (CNG) to use as vehicle fuel, must be wary of siloxanes and monitor the levels. This is because when combusted, siloxanes convert to SiO2, which deposits as essentially a layer of glass inside the engine cylinders used to produce electricity or fuel vehicles. These deposits degrade engine performance and will eventually cause damage to the engine and plug heat exchangers, cause flame sensors in HVAC systems to fail, and damage fuel cells and other equipment in the natural gas pipeline network.
Since it is the silicone (Si) that is of concern, and each siloxane species has a different mass of silicone, pipeline gas quality specifications typically set a limit on siloxanes in the form of mg Si/m3. It is important to note that even if the pipeline gas quality specification or tariff does not set a limit or specifically require monitoring of siloxanes, it is very common that a merchantability clause specifies that the gas shall not contain any other substance which might interfere with the marketability of the gas, or with proper operation of the lines, meters, regulators, or other appliances through which it flows. This then puts the risk back on the producer to ensure siloxanes do not contaminate the natural gas pipeline network, something which has, unfortunately occurred across North America.
Due to these concerns, scrubbers are typically installed to remove siloxanes from the gas prior to use, and siloxane measurements must be taken to determine when to replace this expensive scrubber material.
Continuous Siloxane Monitoring
While historically siloxanes have been difficult and expensive to measure due to the complex and varying gas matrices, Ohio Lumex has developed a proven, reliable, and cost-effective technology to continuously monitor the siloxanes species of concern. Installing these continuous monitors allows the facility to maximize the scrubbing material without risking damage downstream.
The Ohio Lumex Ei2300 Siloxane Monitoring System measures the concentration of individual siloxane species in a sample gas matrix, and allows the operator to see when the lighter weight species begin to break through the scrubber media, indicating replacement is needed. The analyzer reports the individual siloxane species concentrations, as well as total siloxanes concentration, total SiO2, and total Si, and is supported by two well-respected international standards bodies, ASTM via Standard D8455, and ISO via Standard 2613-2:2023.
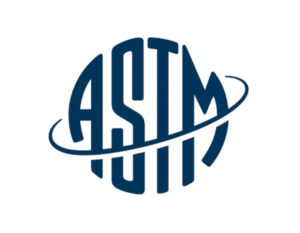
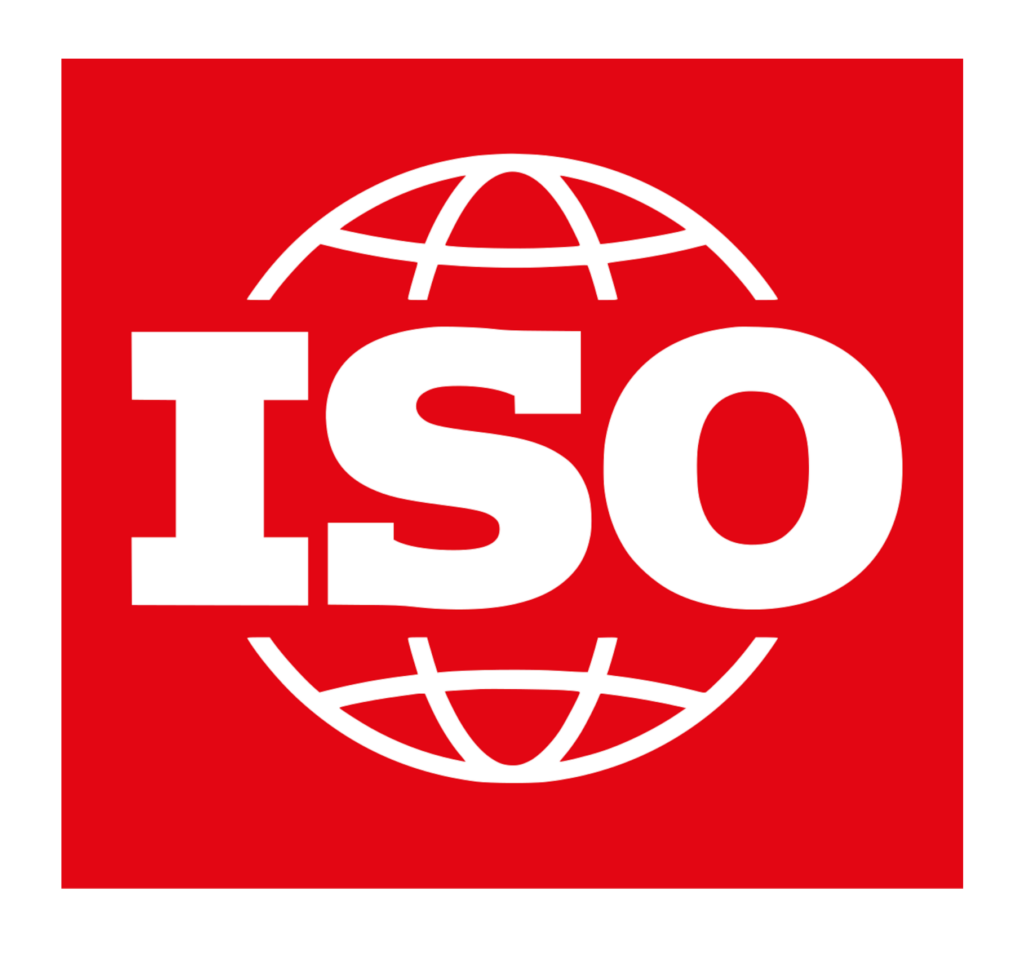
Onsite Sampling and Laboratory Analysis
Ohio Lumex also offers onsite gas sampling and laboratory analysis to determine the concentration of these siloxane species, which is typically required by pipeline interconnection gas quality specifications before gas is allowed to flow. Sampling is performed onsite by our certified technicians, and analyzed in our accredited laboratory on state-of-the-art GC-MS instruments, according to ASTM Standard D8230.
Ohio Lumex is well known for its siloxane expertise and we look forward to supporting you with your specific application needs.