Biogas and RNG sampling is complex, with many common errors leading to concerns about the reliability of analyte concentrations reported. To help alleviate some of these concerns and address common areas of confusion, Ohio Lumex publishes a blog series focused on best practices for biogas and RNG sampling. This edition will focus on sulfur sampling and analysis in raw biogas.
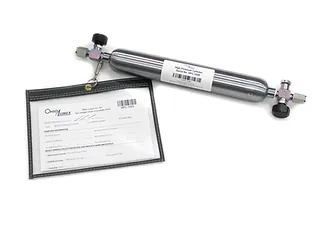
The analysis of sulfur compounds in gaseous fuels is essential to the production, distribution, and regulation of these gases, but the reactivity of sulfur compounds poses a significant challenge to the accuracy and reliability of this analysis. ASTM Standard Test Methods for sulfur determination (D5504 and D6228) stress the importance of both appropriate sampling conditions and the timely analysis of samples to minimize the deterioration that occurs between sampling and analysis. Specifically, it is essential to use inert/passivated containers for collecting and transporting samples, and samples should be analyzed as soon as possible – within 24 hours is preferred, but this is not always realistic due to logistics and expediting costs. To meet these needs, Ohio Lumex has been collecting pressurized gaseous fuels samples in stainless steel high-pressure cylinders with a chemically inert coating applied to the cylinders and fittings. For the analysis of Renewable Natural Gas (RNG), this has been an effective method of preserving samples for sulfur analysis. Â
Raw Biogas
However, there have still been issues with stability for the sampling of raw biogas. Raw biogas typically contains high amounts of hydrogen sulfide (H2S), which is especially reactive among sulfur compounds. Studies conducted by Ohio Lumex have shown that even if a high-pressure cylinder (HPC) has an inert coating, samples initially containing significant H2S can drop below detectable levels in just a few days. Improved turnaround times can help ensure samples are analyzed before complete H2S deterioration, but there are still logistical limitations, and repeat analyses have shown that some raw biogas samples deteriorate quickly even in the first 24 or 48 hours after sampling.
Investigation
Initially, we suspected that this rapid deterioration was due to a reaction between H2S and oxygen, which is typically present at around 1% concentration in raw biogas. However, while testing did confirm the higher concentration of oxygen in raw biogas does contribute to the deterioration of H2S over time, data showed it could not explain the extremely rapid drop in H2S concentration observed in field samples.
Next, we tested the hypothesis that moisture in the sample gas was responsible for the loss of H2S. Raw biogas is typically saturated with water vapor, and we theorized that the change in gas conditions after sampling caused condensation within the cylinder. Specifically, pressurizing raw biogas and/or a decrease in sample temperature was causing condensation within the cylinder. The vapor pressure of water is independent of the total pressure in the container, and thus additional water beyond 100% humidity would return to liquid phase. The condensed water could then be responsible for the increased rate of H2S degradation as it provides a site for reactions to occur more quickly than in the gas phase.
Conclusion
Our testing demonstrated that liquid water in the sample container can have a rapid impact on the concentration of H2S in a gas sample. Under such moist conditions, even if a nonreactive container is used and sulfur analysis is performed within 24 hours of sampling, the H2S in the sample will already have significantly deteriorated. For example, our testing showed an unacceptable H2S loss of more than 83% before the 24-hour mark.
Thus, it is clear that accurate sulfur analysis for raw biogas samples requires care to prevent condensation inside the sample container. However, this can pose a problem when high-pressure cylinders are used as the sampling method. Even at only a portion of the maximum humidity, pressurizing raw biogas (and water vapor along with it) into a HPC can push the relative humidity to 100% and cause condensation. Furthermore, because raw biogas sources are typically at higher temperatures than the ambient conditions the sample is exposed to during transportation and at the location where the sample is analyzed, it is even more likely that the gas temperature will drop below the dewpoint and condensation will occur before sulfur analysis is performed.
Solution
To prevent condensation from affecting H2S results for raw biogas, a sampling system must be used that does not require pressurizing the sample gas and will prevent the sample gas from condensing even as the ambient temperature the sample is exposed to before analysis is lowered.
The solution is to take and store raw biogas samples at below atmospheric pressure, using a container such as a SUMMA canister. With this method, humid gas will resist condensation – even if the temperature changes – because the low-pressure sample will have a lower humidity in the canister, and thus a lower dewpoint.
Ohio Lumex has switched to using SUMMA canisters for sulfur samples at raw biogas sources. Samples taken this way must be pressurized with nitrogen just prior to analysis, which does introduce a slight dilution. Yet they provide much more reliable data on H2S concentration, which is often the most significant sulfur compound by far in raw biogas. This change has ensured that H2S will remain in these samples, and not deteriorate before they can be analyzed – even in cases where it takes several days for the sample to reach the analytical laboratory. Stability is the key to accurate sulfur analysis, and the use of SUMMA canisters has proven crucial in providing reliable data for H2S concentration in humid gas samples.Â
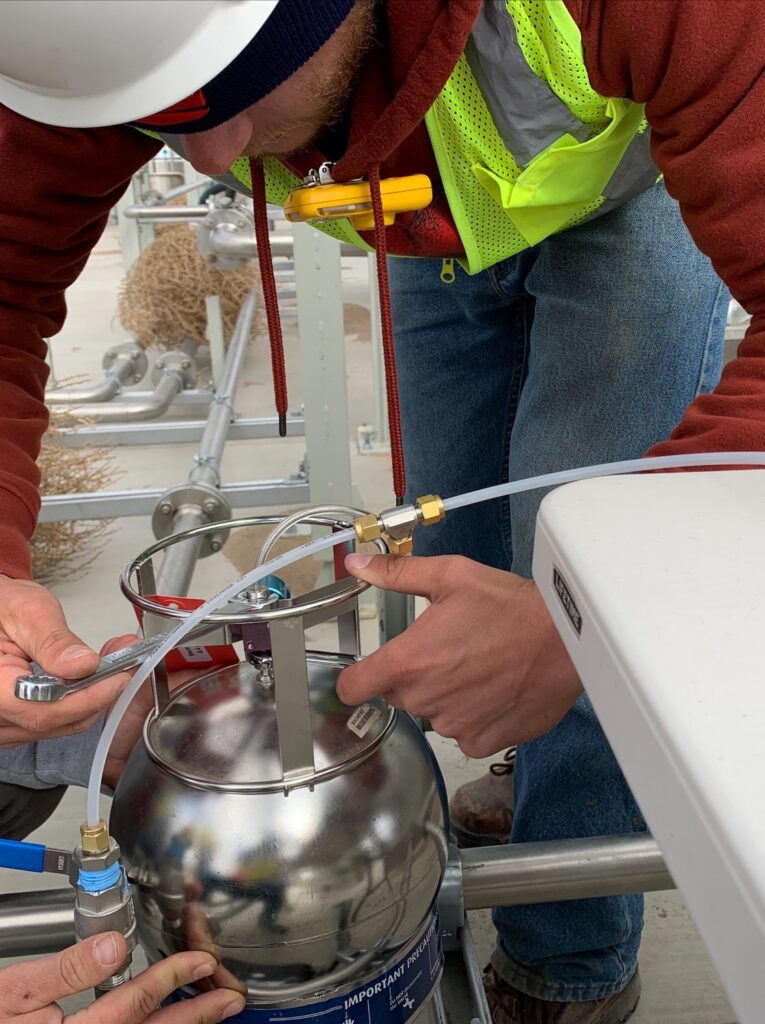
For a copy of our white paper on this subject, please click this link. Since both ASTM Standards D6228 and D5504 do not specifically address the unique sampling and analysis needs associated with raw biogas, Ohio Lumex will be submitting revisions to these standards to ASTM for consideration.
At Ohio Lumex, we are well-known throughout the industry as the leader in biogas/RNG sampling, analysis, and continuous monitoring. We design and produce our own sorbent traps and sampling equipment, and have state-of-the-art laboratory instruments to conduct analysis, helping to ensure our customers have the most accurate results to report for their RNG compliance and address issues in their process.
This is the 6th in a series of posts in which we discuss best practices for biogas and RNG sampling. To learn more about Ohio Lumex biogas and RNG analysis services, please visit our website. Have questions? Contact Bennett Rubin and he’ll be happy to discuss it with you.
Want to read (or re-read) a previous article in the series?
- Biogas/RNG Sampling Best Practices: Volume Correction
- Biogas/RNG Sampling Best Practices: Moisture Sampling and Analysis
- Biogas/RNG Sampling Best Practices: Siloxane Sampling and Analysis
- Biogas/RNG Sampling Best Practices: Mercury Sampling and Analysis
- Biogas/RNG Sampling Best Practices: Oxygen Sampling and Analysis