Biogas and RNG sampling is complex, with many common errors leading to concerns about the reliability of analyte concentrations reported. To help alleviate some of these concerns and address common areas of confusion, Ohio Lumex is publishing a series of blog posts focusing on best practices for biogas and RNG sampling. This fourth edition will focus on another error prone subject: Mercury sampling and analysis. Mercury is another major concern for natural gas pipeline operators, as it is detrimental to pipeline integrity, human health, and end-use equipment. More recently, the growth of Liquified Natural Gas (LNG) exports has put additional focus on mercury since it can lead to the failure of the aluminum cryogenic heat exchangers used to convert natural gas to LNG. Several natural gas pipelines feeding the LNG Terminals on the Gulf Coast have installed Ohio Lumex Continuous Mercury Monitors for just that reason.
Mercury Sorbent Traps
The industry standard for sampling and analysis of mercury in gaseous fuels is ASTM D5954, which was updated last year. Here, sorbent traps with gold coated beads are used to collect the mercury for analysis. Two sorbent traps are sampled in series, where the first trap is the primary, and the second trap is the breakthrough trap. Common errors we see here are not indicating on the Chain of Custody which sorbent trap was the primary and which was the breakthrough, or sampling the two traps in parallel instead of in series.
All Wetted Surfaces Should be Inert
One of the most common issues with sampling and analyzing mercury is that it is very reactive, including with silicone and metals such as stainless steel, which will scrub mercury and bias the results low. It is therefore critical that you use PTFE, FEP, or passivated stainless steel lines, and that all other metal surfaces that interact with the sample gas have inert coatings as well. This includes:
- Probes
- Regulators
- Valves
- Sample lines
- Fittings
Use New/Cleaned Sampling Components
Another common mistake is not using new PTFE sample lines, and not cleaning all sampling valves, fittings, etc. prior to the sampling project. In this case, mercury that has deposited on the surfaces from prior projects can bias the results high, potentially jeopardizing compliance with RNG interconnection gas quality specifications. Conversely, mercury can be scrubbed by fouled/reactive surfaces, thus biasing the result low.
Handling
Contamination from handling is another common problem due to the extremely low mercury concentrations (ppb or ppt levels) being measured. All mercury sorbent traps and sampling components should be handled with clean nitrile gloves and properly packaged to prevent contamination.
Raw Biogas Sampling raw biogas introduces additional issues, generally related to moisture. It is critical to limit moisture condensation along the sample train, especially inside of the mercury sorbent traps. With RNG that is not an issue as the moisture content is extremely low. However, with the high moisture typically associated with raw biogas, a portion of the sample train must be heated, or moisture removed upstream of the mercury sorbent traps without compromising sample integrity.
At Ohio Lumex, we are well known throughout the industry as the leader in mercury sampling, analysis, and continuous monitoring. We design and produce our own mercury sorbent traps and sampling equipment, and have state-of-the-art laboratory instruments to conduct analysis, helping to ensure our customers have the most accurate results to report for their RNG compliance, and address issues in their process.
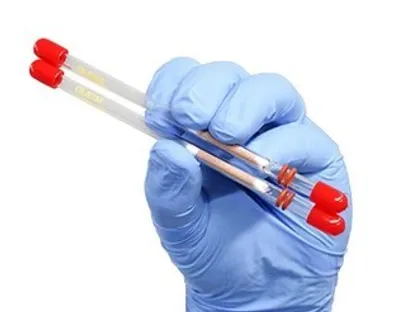
This is the fourth in a series of posts in which we discuss best practices for biogas and RNG sampling. To learn more about Ohio Lumex Biogas/RNG Analysis Services, please visit our website. Want to re-read a previous article in this series? Please visit the links below.