Renewable natural gas (RNG), also known as biomethane, is a carbon-neutral fuel that can be used as an alternative to fossil natural gas. RNG is produced by upgrading biogas to meet defined quality standards, after which it may be distributed via the existing gas grid or sold as an alternative fuel source for vehicles in the form of compressed natural gas (CNG). As a result of various government incentives, federal and state renewable energy targets, and an increase in public demand to reduce greenhouse gas emissions, RNG production has increased in recent years and is projected to grow substantially (ref 1). In its December 2019 report, the American Gas Foundation estimated upper and lower bounds for growth in RNG production over the next 20 years (Figures 1 and 2) (ref 2).
Figure 1 – Estimated Annual RNG Production, Low Resource Potential Scenario, tBtu/y
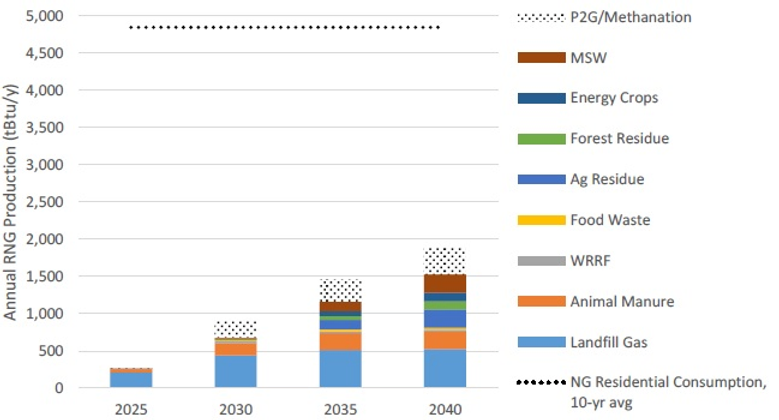
Figure 2 – Estimated Annual RNG Production, High Resource Potential Scenario, tBtu/y
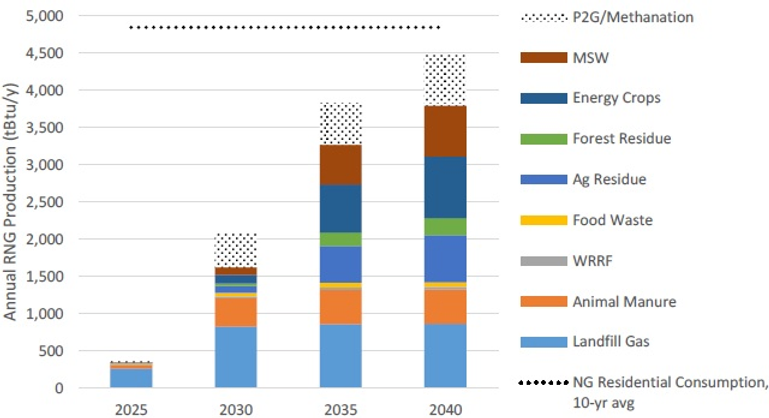
The gas used to create RNG is derived from methanogenic decomposition of organic materials such as landfill waste, sewage sludge, crop waste, manure, and food waste. This raw biogas generally contains 45-65% methane with varying concentrations of moisture, particulate, O2, N2, VOCs, H2S, and siloxanes – depending on the source feedstock. Raw biogas must go through a series of treatment stages before it is suitable for biogas applications, and another series of treatment stages to produce RNG. An example of this process applied to landfill gas is illustrated below (Figure 3).
Figure 3 – EPA LMOP Diagrams of RNG Sources, Gas Treatment, and End Uses (ref 3)
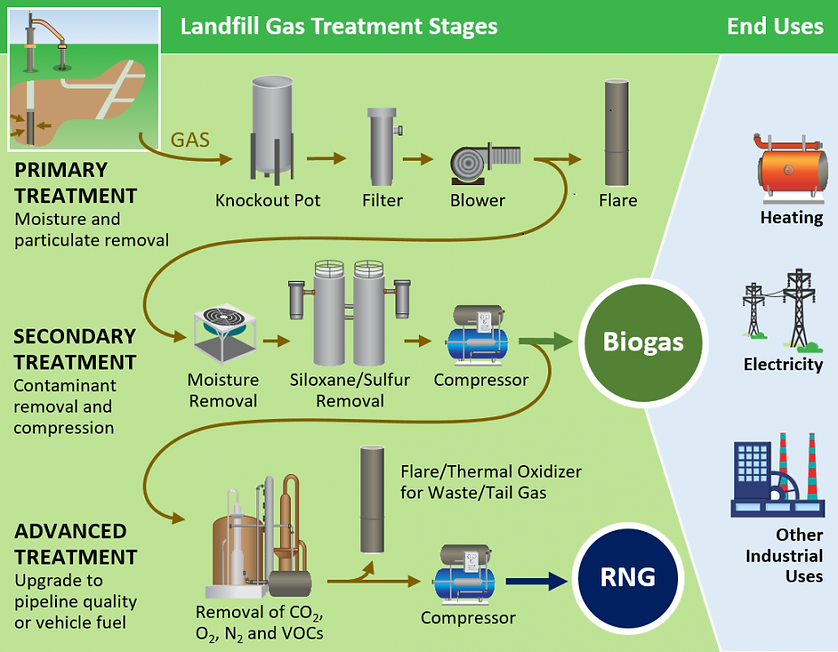
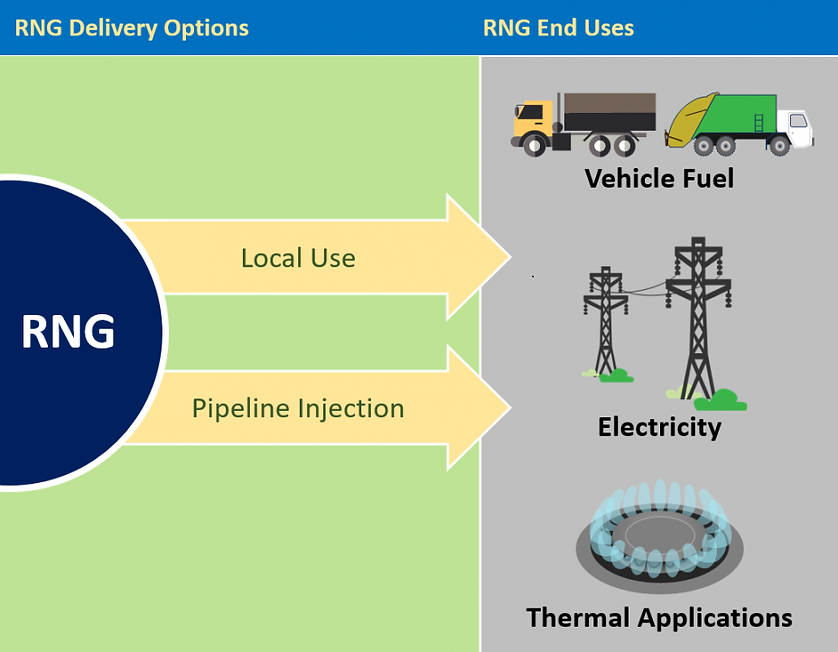
For biogas and RNG suppliers, operation and maintenance costs associated with gas treatment equipment can be significant. In some cases, these costs could present a barrier to entry for potential suppliers (ref 4). It is, therefore, critical for suppliers (or contracted equipment operators) to optimize the maintenance cycle for each stage of the gas treatment process. By doing so, a supplier may minimize maintenance or material replacement frequency while simultaneously adhering to the required gas quality standards for its application.
Suppliers must adhere to quality standards that establish upper limits of total silicon in the final gas product. Typically, a carbon-based adsorbent material is used to remove siloxanes from its gas stream. Instead of establishing an arbitrary (or roughly estimated) material replacement schedule, the supplier can optimize the replacement frequency to minimize operating costs. They do this by continuously measuring the siloxanes’ concentration in the gas. With these data, the supplier finds they can reduce the material replacement frequency by waiting for the concentration to reach 90% of its quality standard limit (0.09mg/m3).
Figure 4 – Siloxanes Breakthrough Curves Under Arbitrary and
Optimized Material Replacement Cycles
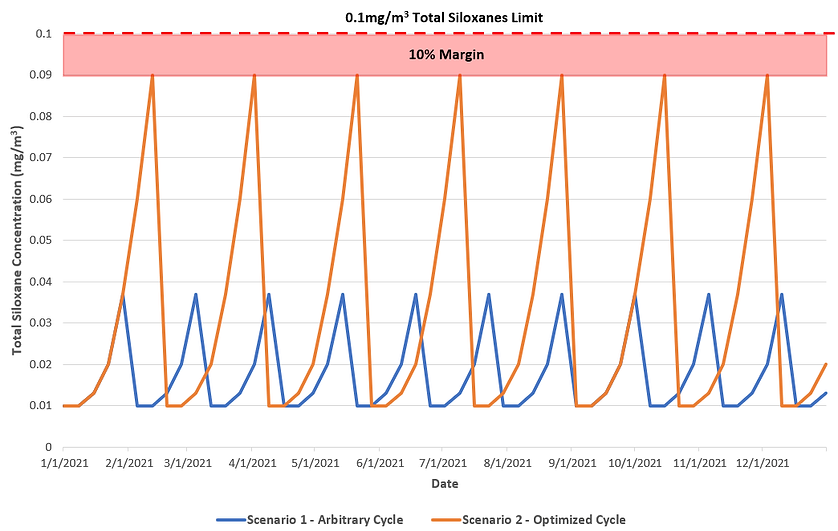
Frequent measurement of gas composition is critical for optimization of the treatment process. The advantages of frequent measurements are particularly pronounced in the case of siloxanes, as these compounds tend to grow in concentration very rapidly once they begin to break through scrubbers. Failure to control siloxanes can have significant consequences for both suppliers and consumers, depending on the application. For facilities that use gas engines to produce electricity, combustion of siloxanes can form a layer of silicon dioxide (SiO2) on the interior of the engine’s cylinders – resulting in eventual failure (Figure 5).
Figure 5 – Silicon Dioxide Deposition in a Gas-to-Energy Engine
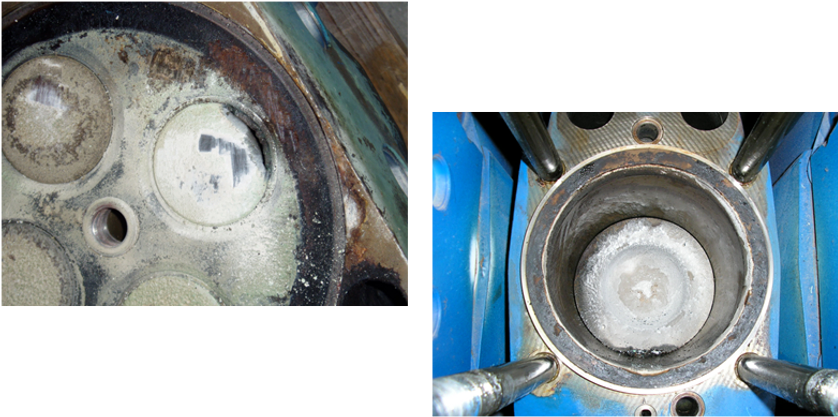
For RNG suppliers, whether the gas is used for CNG vehicles or injection to the gas grid, siloxanes must be removed. CNG vehicle engines face the same SiO2 deposition problem as gas-to-energy facilities. If siloxanes in RNG are added to the gas grid, residential and commercial furnaces may be compromised by the accumulation of SiO2 on flame sensors, condenser coils, and other components (ref 5). As RNG production increases and more suppliers want to sell their gas to utilities, some utilities have started requiring RNG suppliers to ensure their siloxanes are below a certain concentration before the gas can be injected into a distribution system. Two examples of such utilities are PG&E and SoCalGas.
PG&E’s Electric Rule 21 and SoCalGas’ Rule 30 are very similar, and they establish what are called a “lower action level” (LAL) and “trigger level” (TL) for siloxanes in RNG. The limits for both rules are currently 0.1mg Si/m3 for the LAL and 0.01mg Si/m3 for the TL. These levels are used to define specific frequencies at which suppliers must measure their gas composition. Regarding siloxanes, the majority of affected RNG suppliers are those connected to landfills or wastewater treatment plants. Siloxanes are man-made compounds and are present in many commercial and industrial products that end up in municipal solid waste or wastewater. Both Rule 21 and Rule 30 specify reduced siloxane testing requirements for biomethane derived from other sources, such as dairy or other animal manure, agricultural waste, forest residues, and commercial food processing waste, provided the RNG Supplier can certify there are no siloxane-containing products used in the facility in a way that could affect the product. The differences between reduced testing requirements and standard testing requirements can be understood by examining Figure 6 below.
Figure 6 – Reduced and Standard Testing Requirements for Siloxanes in RNG – per Rules 21 and 30
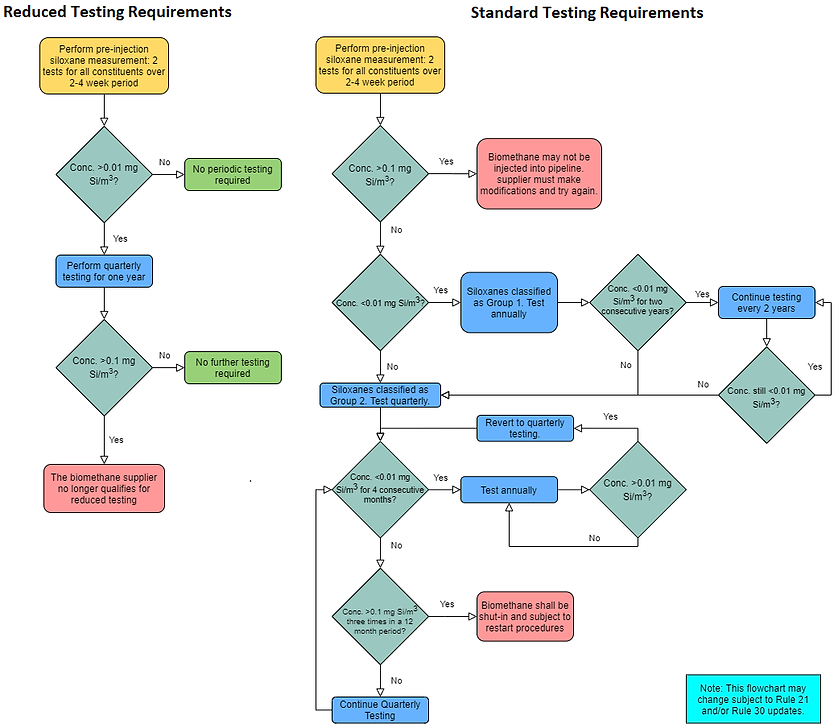
There has been some debate within the industry regarding whether siloxanes can be measured at these low concentrations. In 2018, the California Council on Science and Technology produced a report in which the researchers determined “at present, no standardized measurement protocol exists for dependable measurement of the 0.1mg Si/m3 specification” (ref 5). To address this lack of a standardized measurement protocol, ASTM Method D8230-19 was recently created. It lists GC-AED, GC-MS, and ICP-MS as suitable methods for laboratory analysis of samples collected from biogas/RNG production facilities (ref 6). Although a small number of commercial labs have started reporting limits that can meet the requirements described in Rules 21 and 30, most cannot.
The difficulty in accurately measuring siloxanes is only partially a result of the required analytical sensitivity. As many in the industry know very well, there are problems with the common methods of sample collection. Many biogas and RNG suppliers around the country are currently using Tedlar bags or passivated stainless steel canisters (these canisters must be passivated with a fused-silica lining). However, less volatile siloxanes may adhere to the interior of both Tedlar bags and canisters, resulting in incomplete recovery of siloxanes when transferring gas from vessel to analyzer (ref 5). SCS data indicates the majority of siloxanes in landfill and digester gas are D4 and D5, and both species have low volatility (ref 7). As a result, there is a risk that a significant fraction of D4 and D5 will remain on the interior surface of Tedlar bags or canisters, preventing these species from being measured at their true concentration. In addition, there is evidence of siloxane recoveries degrading rapidly in Tedlar bags, which is why ASTM D8230-19 recommends analysis be completed within 72 hours. Finally, some Tedlar bags may contain silicone-based materials (primarily in the valve stem) that introduce siloxanes to the sample gas, leading to a high measurement bias (ref 8). Along with a series of real gas samples, Ohio Lumex sent a Tedlar bag filled with pure nitrogen gas to a laboratory to serve as a field blank. The laboratory reported a total siloxane concentration of 0.29mg Si/m3 in the field blank, which was similar to the concentration measured in the real gas samples.
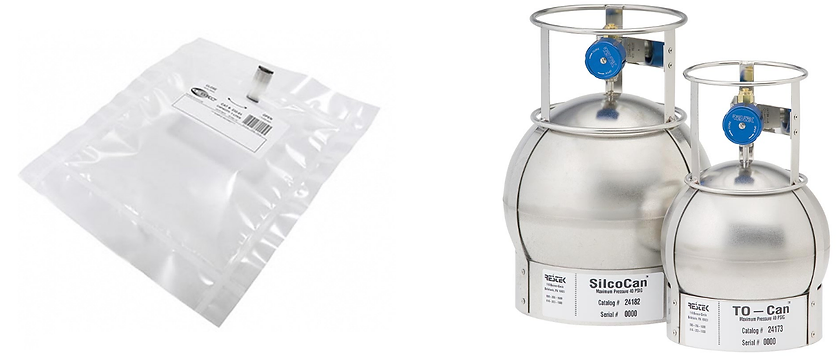
ASTM D8230-19 includes sampling methods using Tedlar bags, passivated canisters, and sorbent traps. Given the complications with Tedlar bags and passivated canisters, sorbent traps may seem to be the ideal sampling method. However, the procedure described in the ASTM method calls for sample extraction using methylene chloride, and there are concerns regarding matrix interferences from either the extraction solvent or the sorbent material itself. The sorbent trap approach holds promise, but the method needs to be simplified and designed to be as accurate as possible. To this end, Ohio Lumex is actively developing a user-friendly sampling technique and thermal desorption method for siloxane sorbent traps. When this method is complete, it will be put to the ASTM D03 committee for inclusion in D8230-19. The objective is to provide users with a complete sampling and analysis procedure with none of the risks of bias inherent with the previously discussed sampling and analysis methods.
Given the previously discussed benefits regarding optimization of scrubber material replacement as well as the challenges associated with sampling and analysis of siloxanes, one may conclude the best solution is to use a continuous online siloxane analyzer. Until recently, online siloxane analyzers were unable to reliably meet the sensitivity requirements of Rules 21 and 30 (ref 9). However, in 2019, Ohio Lumex introduced a new analyzer to the industry, which is affordable, extremely sensitive, and highly selective for all siloxane species. This analyzer utilizes gas chromatography coupled with an ion mobility spectrometer, or GC-IMS. By applying two dimensions of separation to the constituent compounds, the analyzer provides excellent sensitivity for every siloxane species, without matrix interferences.
In addition, an integrated sampling system with heated sample line assures the instrument receives a representative and timely sample, and a purged enclosure suitable for Class 1 Division 2 hazardous rated areas is available for RNG facilities that require it.
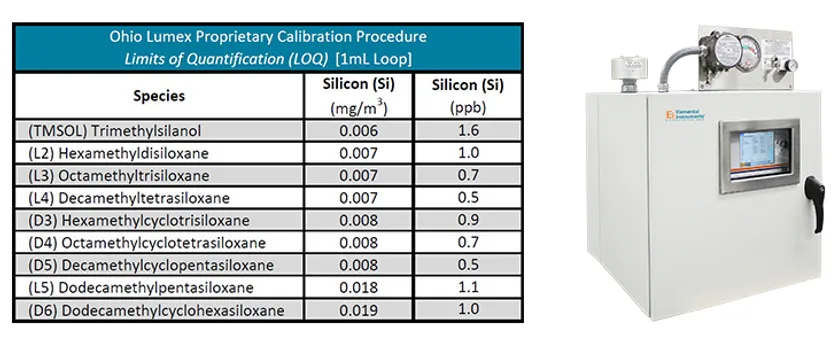
The GC-IMS provides speciated and total siloxane measurement data up to once per hour, allowing for near real-time determination of scrubber performance and gas quality. Most GC-IMS users will find it sufficient to collect one or two measurements per day, which is far better than relying on quarterly or annual measurements using Tedlar bags or canisters, especially when those sampling methods may produce biased results. The analyzer produces three-dimensional chromatograms (GC retention time, IMS drift time, and intensity of instrument response) that allow the user to visually observe how their gas composition changes over time, as demonstrated in the animation below.
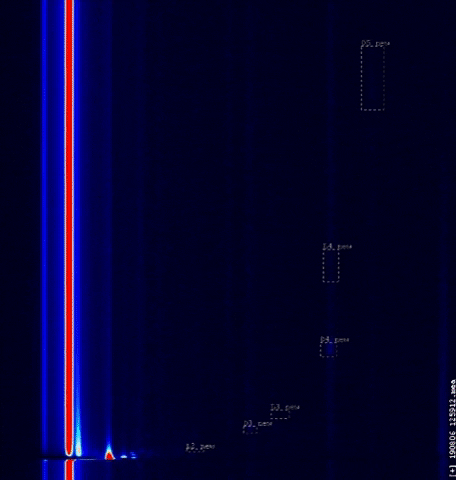
With the Ei2300 Siloxane Continuous Monitoring System, a biogas or RNG supplier will have the ability to measure siloxanes at the low concentrations required by Rules 21 and 30, while also optimizing scrubber material replacement through nearly continuous measurements of breakthrough.
If you have any questions regarding the Ohio Lumex GC-IMS for siloxanes, please contact Bennett Rubin and Jonathan Cross at bennett.rubin@ohiolumex.com and jonathan.cross@ohiolumex.com
References
1. Bates White Economic Consulting. Renewable Natural Gas Supply and Demand for Transportation. April 2019.
2. American Gas Foundation. Renewable Sources of Natural Gas: Supply and Emissions Reduction Assessment. December 2019.
3. U.S. Environmental Protection Agency. Landfill Methane Outreach Program: Renewable Natural Gas. March 2020. https://www.epa.gov/lmop/renewable-natural-gas
4. Johnston, Marsha. Breaking Down Renewable Natural Gas Injection Barriers, Biocycle. March 2020. https://www.biocycle.net/2014/09/18/breaking-down-renewable-natural-gas-injection-barriers/
5. California Council on Science & Technology. Biomethane in California Common Carrier Pipelines: Assessing Heating Value and Maximum Siloxane Specifications. June 2018.
6. “Standard Test Method for Measurement of Volatile Silicon-Containing Compounds in a Gaseous Fuel Sample Using Gas Chromatography with Spectroscopic Detection” ASTM International, West Conshohocken, PA, 2019, DOI: 10.1520/D8230-19, www.astm.org.”
7. Wheless, Ed, and Jeffrey Pierce. Siloxanes in Landfill and Digester Gas Update. 27th Annual SWANA LFG Symposium, March 2004.
8. Hayes, H. C., Graening, G. J., Saeed, S., & Kao, S. (n.d.). A Summary of Available Analytical Methods for the Determination of Siloxanes in Biogas.
9. CRNG. (2016). Revisiting CPUC AB 1900 Biomethane Pipeline Injection Regulations to Remove Barriers Preventing Biomethane Project Development in California.