This Article was written by ChatGPT
and edited by Alexandra Sipershteyn & Aaron Fellhauer
Recently coal-fired utilities burning lignite were sent “114 letters” from the EPA requesting Mercury Emissions data. A “114 letter” typically requests information from the recipient regarding their operations, emissions, and may request additional information or documents related to compliance with environmental regulations.
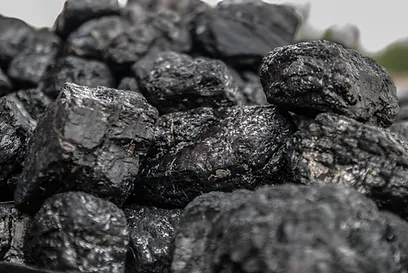
Lignite coal has lower energy content and higher moisture content compared to other types of coal. Additionally, lignite coal is known to contain higher sulfur, ash, and mercury levels. This can have negative impacts on air emissions and subsequently control strategies.
Under the MATS rule, coal-fired power plants are required to meet specific emissions limits for mercury and other toxic air pollutants. The rule sets a national emissions limit for mercury of 1.2 lbs/TBtu for coal-fired power plants, with a lower limit of 0.007 lbs/TBtu for lignite-fired plants. It is worth noting that the MATS rule has faced legal challenges and regulatory changes in recent years, so the specific mercury limits for coal-fired power plants may be subject to change in the future.
Oh ChatGPT…WRONG! We know that the limit for lignite plants is actually 4.0 lbs/TBtu!!
But, I think you may be right on the second part…
With the remittance of the 114 letters, it is hypothesized that lignite burning facilities may have a reduced emissions limit for mercury and thus may be required to control mercury emissions to 1.2 lbs/TBtu like other utilities burning bituminous and subbituminous coals.
So, where does that leave us?
TESTING!!!
If you must reduce Hg, what should you evaluate to point you in the direction of the best control strategy?
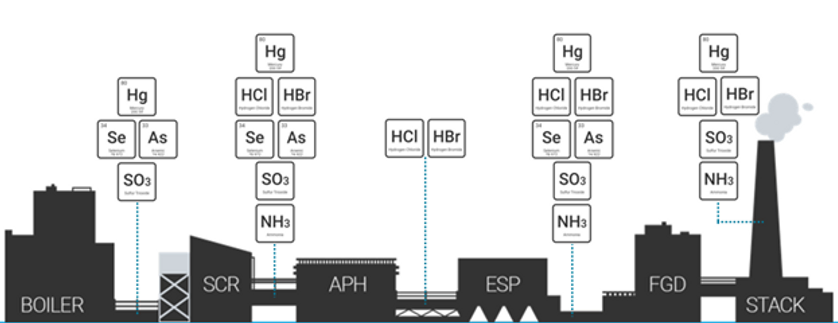
Although there are many relevant measurements, for the purpose of this post let’s concentrate on the most crucial ones for lignite, which are also applicable to utilities using other coal types.
What type of mercury are you dealing with?
If you see a metallic river, either you’re in an ancient Chinese Emperor’s tomb or you have a serious problem. Unfortunately looking for mercury is not typically this simple in a flue gas application. So we must first define what exactly we are looking for to properly evaluate mercury in any setting where coal is used as a fuel source. There are, like most elements, two common states of mercury. There is oxidized mercury which is the good kind because it is water soluble, making it easy to take out of the flue gas. Then there’s elemental mercury, which is much more difficult to deal with.
Since oxidized mercury is water soluble, we can remove it from the flue gas when the gas itself goes through a source of water such as a Wet Flue Gas Desulfurization (FGD) unit. What is left is elemental mercury. Elemental Hg can be taken care of by expensive injections or by oxidizing it and then removing the oxidized mercury through traditional means.
Understanding the concentrations of oxidized and elemental mercury at the inlet of the FGD is the MOST important measurement!
This measurement tells you whether you have potential to oxidize more mercury and thus you should move your control strategy upstream.
OR
If you should focus your attention on activated carbon injection or the FGD itself.
Unfortunately, this measurement can be challenging if you are attempting it with those crazy impinger trains like the Canadians…ie. Ontario Hydro. We typically perform these measurements with modified Method 30B using Speciation Sorbent Traps. You still must know what you’re doing, so hit me up (Alexandra) to get the SOPs for sampling and analysis!
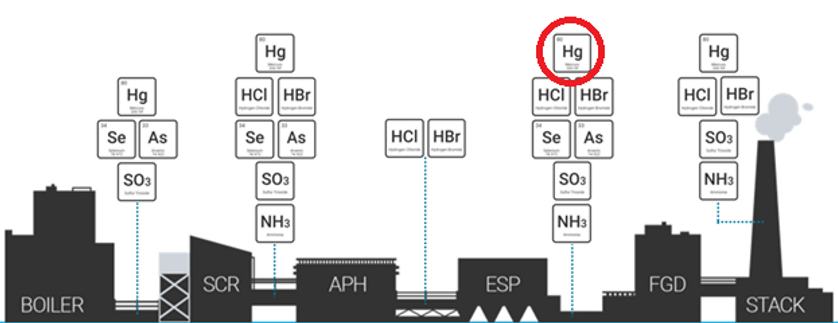
If you are seeing less than 95% oxidized Hg, then you have potential for greater oxidation!
So, how do we convert most of the mercury into oxidized mercury?
We tried asking nicely, but I’m afraid to report that this mercury control strategy was seldom successful which forced us to resort to other tactics.
One way to treat the byproducts from burning coal is to pretreat the coal itself before burning. Most commonly, halogenated ionic compounds such as Calcium Bromide or Potassium Iodide are sprayed onto the coal to allow for greater oxidation of mercury making it easier to remove with existing technologies.
Measuring the concentration of oxidized and elemental mercury at the outlet of the boiler helps to guide the effectiveness of this injection strategy.
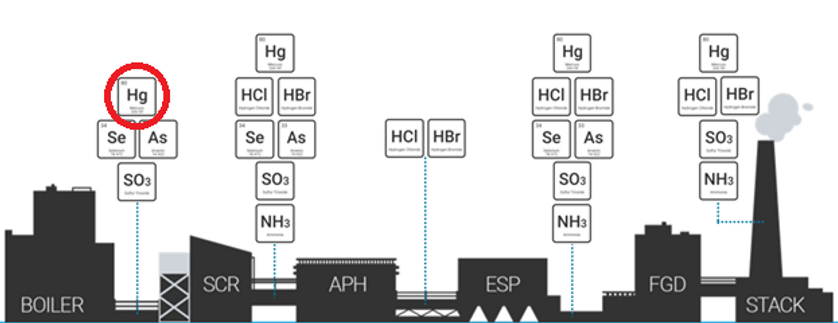
This is a challenging measurment because of the high concentration of halogens and particulate as well as high temperatures. Yet, with a little elbow grease and some knowhow, it can be done with speciation sorbent traps and a cooling probe. We recommend performing a breakthrough study before sampling comenses and if you are not sure what that is…contact me (Alexandra).
What else increases Hg oxidation?
Many utilities operate SCRs (Selective Catalytic Reduction) for Nitrogen Oxide (NOx) control but appreciate its co-benefit of mercury oxidation. The SCR catalyst typically consists of a porous material such as titanium dioxide that is coated with metal oxides like tungsten or vanadium which create the active catalytic sites. The SCR catalyst works by facilitating the reaction between nitrogen oxides (NOx) and ammonia (NH3) to form harmless nitrogen and water vapor.
The same metal oxides that promote the NOx reduction reaction can also catalyze the oxidation of Hg to its oxidized forms. This happens because the metal oxides on the surface of the SCR catalyst can adsorb elemental Hg, which then reacts with oxygen (O2) in the flue gas to form HgO which can then react with halogens in the flue gas to form mercuric salt compounds. Shesh….that was a mouthful!
The important take away is that you can gauge the effectiveness of the SCR to oxidize Hg as the catalyst layers age by measuring the concentration of oxidized and elemental mercury at the inlet and outlet of the SCR.
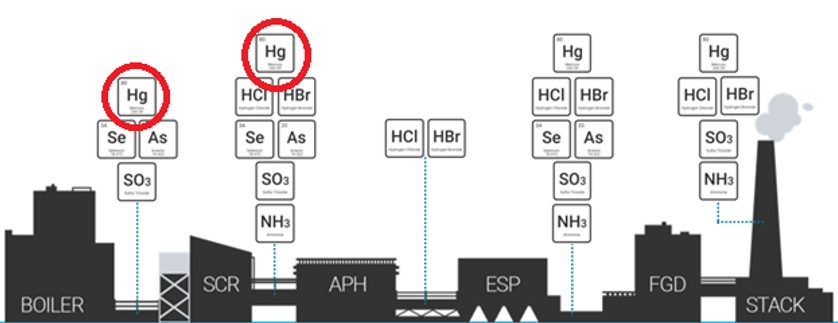
While high concentrations of halogens and particulate as well as high temperatures are present in this location as well, when there’s a will there’s a way! We have developed optimal sampling parameters so speciation sorbent traps and cooling probes can effectively be used for these SCR efficiency evaluations. We also recommend a breakthrough study at both locations prior to testing.
Does the mercury oxidation potential of the SCR change over time?
YES!!! Over time, as SCR catalyst layers age, the catalyst deactivates. In addition, ammonia bisulfate formation can take up the active sites on the catalyst. Periodically performing speciation studies (like the one described above) can provide an indication of decreasing catalyst efficiency as it pertains to mercury oxidation over time. This can be an excellent tool to add to an SCR management plan.
There is one more important factor to keep in mind here. To combat catalyst deactivation, greater amounts of ammonia are required to be used until the plant is ready to clean the catalyst or replace a layer. Unfortunately, this increased use of ammonia can result in ammonia slip.
But, many lignite plants utilize an SNCR for deNOx…why would they care?
Because ammonia is a big deal!!!
Ammonia or urea is used by lignite coal burning utilities to operate Selective Non-Catalytic Reduction (SNCR) systems for NOx control. The reduction efficiency of SNCR depends on several factors, including the temperature of the flue gas, the concentration of NOx, the type of reagent used, and the injection location and distribution. SNCR systems tend to have higher ammonia slip compared to selective catalytic reduction (SCR) systems. SNCR systems require careful monitoring and control of the ammonia injection process to prevent ammonia slip.
Since both SCR’s and SNCRs use ammonia or urea for the reagent reaction, we need to consider how this affects mercury.
And … the effect is dire!
Excess ammonia can reduce oxidized Hg(2+) (HgCl2, HgBr2, HgI2) back to elemental Hg(0) form.
Elemental Hg is much more difficult to remove with traditional control technologies (as we know) so this reduction reaction poses a big problem for mercury control!
One of our next blog articles will go into much more detail on this subject, so I don’t want to steal its thunder. But it is important for utilities to carefully monitor and control their ammonia levels in order to ensure the effectiveness of their mercury control strategies. Nothing would make me madder than a hunchback in a limbo contest than if I was to implement an expensive mercury control strategy all to find out that the ammonia slip was really responsible for all my problems…well, I guess not aaaaaaaaaall my problems…. ok…I’ll discuss that in therapy.
Still, did you know you can measure your ammonia slip with method 30B style Ammonia sorbent traps? It’s actually one of the easiest sorbent trap methods!
On the other hand, what if you are at 95% oxidized Hg at the inlet of the FGD but still not meeting the limit?
Then go in the opposite direction and evaluate if you are seeing reemissions through your wet FGD.
This is done by measuring TOTAL Hg at the stack and comparing it to the elemental Hg at the inlet of the FGD. If the elemental Hg at the inlet of the FGD is about the same as the total Hg coming out of your stack, then you do not have a reemissions issue. If on the other hand the elemental Hg is less than the total Hg coming out of your stack, reemissions may be to blame and you should evaluate the FGD further. We’re working on a blog article about this topic as well so keep your eyes peeled!
To Recap:
Inlet of FGD elemental Hg < Stack Hg = REEMISSIONS (…most of the time)
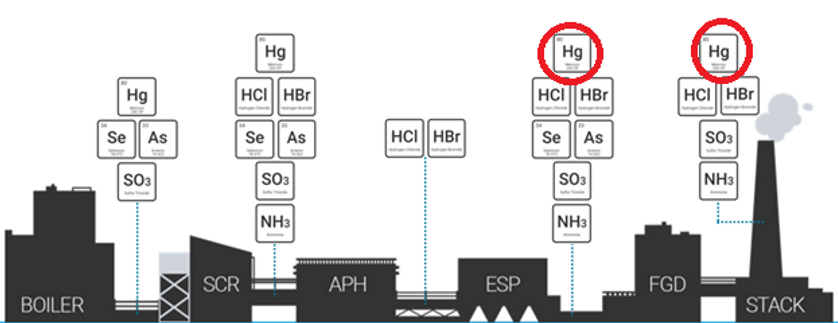
What other control strategies could we consider?
You can investigate FGD additives (which we will discuss in the reemissions blog along with slurry mass balance to help guide your decision-making on which FGD additives to experiment with.) You can also go the traditional route of activated carbon injection or halogenated PAC Injection. We will do a future article on those as well since this post is specifically about flue gas measurements.
Speaking of flue gas measurements, is there anything else we should evaluate in the flue gas that may impact the effectiveness of these strategies?
Measure SO3!!
Sulfur trioxide (SO3) can affect mercury control in several ways. In flue gas, SO3 can react with mercuric compounds [Hg(0), Hg(2+)] to form mercury sulfates (HgSO4), which can then be captured by certain control technologies such as wet scrubbers and fabric filters. This can increase the overall removal efficiency of these technologies for mercury, as the mercury sulfates are more easily captured than the gaseous mercury compounds.
However, SO3 can also have negative effects on mercury control in certain conditions. For example, high levels of SO3 in the flue gas can lead to the formation of sulfuric acid (H2SO4), which can corrode the equipment used in mercury control technologies such as activated carbon injection (ACI) and dry sorbent injection (DSI).
Additionally, SO3 may also compete with mercury for adsorption sites on activated carbon and other sorbents, which can decrease the overall removal efficiency of these technologies for mercury.
Overall, the effect of SO3 on mercury control can be complex and depend on many factors such as the concentration of SO3, the form of mercury present in the flue gas [Hg(0) or Hg(2+)], and the type of control technology used. Therefore, it is important for utilities to carefully monitor and control the SO3 levels in the flue gas to ensure the effectiveness of mercury control measures.
Oh … and SO3 also impacts the SCR! Stay tuned for a blog post that explores this in more detail.
SO3 measurements can also be performed with SO3 sorbent traps. This is done Method 30B style most of the time, but not always.
Concluding thought: In the article above, ChatGPT kept coming back to elemental Hg versus oxidized Hg and that control strategies are dependent on the species present.
Did you know that we can speciate Hg in REAL-TIME as you make process changes? With the Portable 915J Mercury CEM, we can be set up in 2 hours and reporting speciation data the next day!
Miss part of the series? Check out a few of our other blog posts on elevated Hg levels: